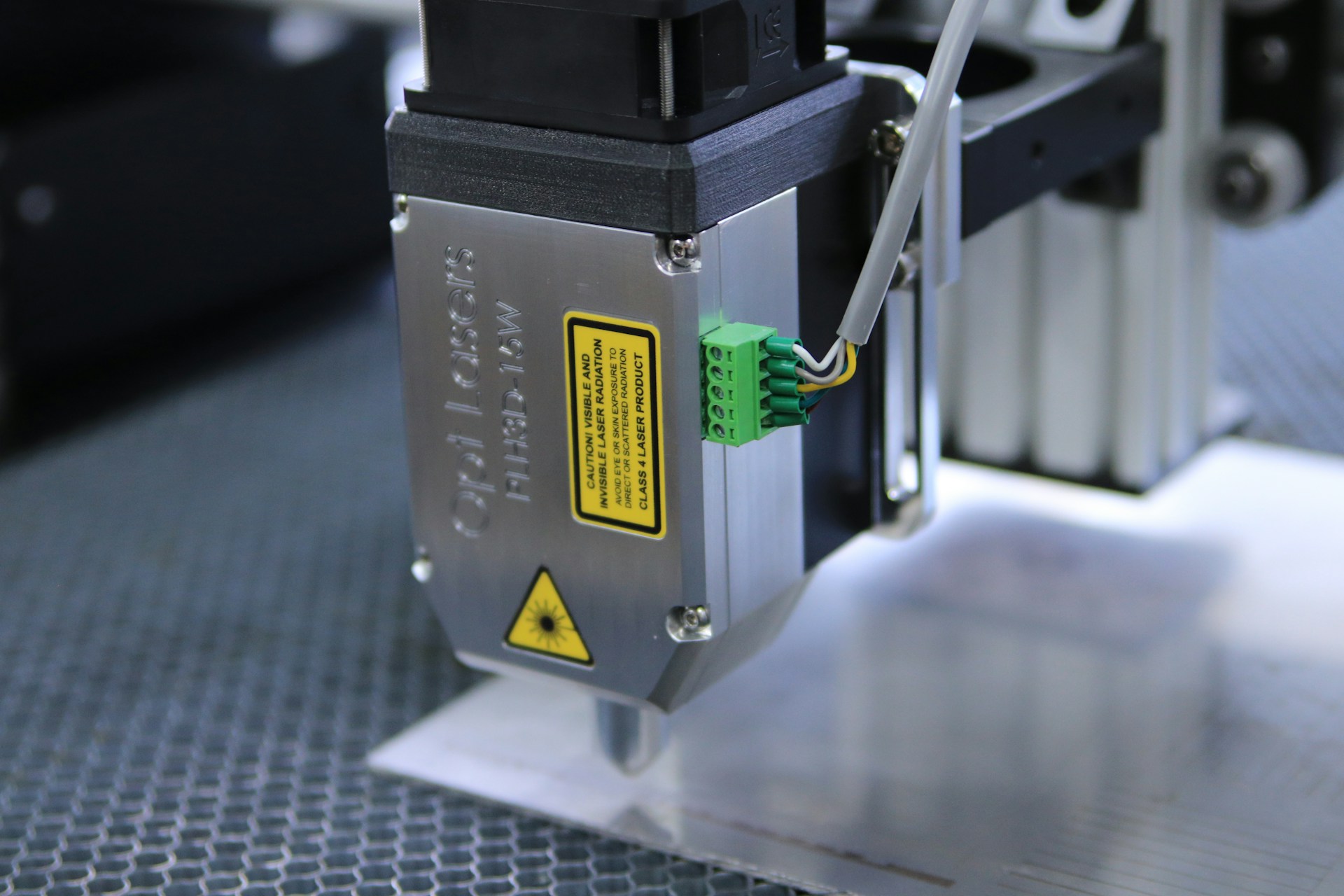
Discover the plastic injection molding process, its benefits, and its applications across industries. Learn about innovations, challenges, and the future of this essential manufacturing method.
Plastic injection molding is an essential manufacturing process utilized across a wide range of industries. This method involves injecting molten plastic into a pre-designed mold to create a variety of shapes and parts. The appeal of this technique lies in its efficiency and ability to produce large quantities of identical items with remarkable precision. As the demand for plastic components grows, understanding the intricacies of injection molding becomes increasingly valuable.
Understanding the Injection Molding Process
The injection molding process begins with melting the plastic material, which can be made from thermoplastics or thermosets. Once the plastic is heated to its melting point, it is injected into a mold cavity under high pressure. The mold itself is typically crafted from metal and designed to the precise specifications of the desired part. Cooling channels within the mold help solidify the molten plastic quickly, allowing for fast production cycles.
Each cycle can take anywhere from a few seconds to several minutes, depending on the complexity of the molded parts and the size of the batch. After the plastic has cooled and hardened, the mold is opened to eject the newly formed plastic component. This method allows manufacturers to produce highly detailed and intricate designs capable of accommodating a wide variety of product requirements. Many industries also leverage the ability to create parts with tight tolerances, ensuring high-quality output.
Key Benefits of Plastic Injection Molding
Plastic injection molding offers numerous advantages that make it a preferred choice for manufacturers. One of the primary benefits is its cost-effectiveness, especially for high-volume runs. The initial investment in molds can be substantial, but when producing large quantities, the per-unit cost decreases significantly. Speed is another important factor; the ability to create parts quickly allows companies to respond rapidly to market demands.
The versatility of materials available for injection molding ensures that manufacturers can choose the best option for their specific application, including various plastic grades and compositions. Another noteworthy benefit is the reduction of waste; the efficient use of material minimizes excess scrap, contributing to a more sustainable production method.
Applications of Plastic Injection Molding
The applications of plastic injection molding span numerous industries, showcasing its versatility and adaptability. In the automotive sector, the process is utilized to produce interior and exterior components such as dashboards, bumpers, and clips. These parts often require meticulous planning and design to ensure they meet stringent safety and regulatory standards. The consumer electronics industry benefits from injection molding for producing lightweight, durable casings and structural components.
Medical devices also frequently employ plastic injection molding, producing critical components like syringes, tubing, and housings for electronic devices. Given the industry’s strict compliance requirements, precision and cleanliness during the manufacturing process are of utmost importance. Toys and household products often utilize this process for creating complex designs that engage users and simplify everyday tasks.
Recent Innovations in Injection Molding Technology
Innovations in plastic injection molding technology have significantly enhanced the capabilities of manufacturers. The development of advanced materials has broadened the types of products that can be created, including composites and biodegradable options. Enhanced computer-aided design (CAD) tools are enabling designers to create mold parts with greater intricacy and performance. The integration of automation and robotics further streamlines production processes and optimizes cycle times.
Many organizations are now implementing Industry 4.0 principles, utilizing IoT devices and real-time data analytics to monitor production and maintain quality control. Such approaches allow for immediate troubleshooting and adjustments, reducing downtime and boosting productivity. Furthermore, advances in mold design, such as conformal cooling channels and multi-cavity molds, improve efficiency and reduce overall costs.
Challenges Facing Plastic Injection Molding
Despite its many benefits, plastic injection molding faces a range of challenges. One significant issue is the high cost of initial mold creation, which can deter smaller businesses from investing in the technology. Since molds require precise engineering, any imperfections can lead to significant expenses for corrections.
Market fluctuations in material prices can influence production costs, affecting profit margins. The growing emphasis on environmental concerns also poses challenges; manufacturers are under increasing pressure to minimize waste and develop sustainable practices. For companies entrenched in traditional methods, adapting to advanced technologies and new equipment can also pose hurdles.
The Future of Plastic Injection Molding
The future of plastic injection molding is likely to be characterized by continued innovation and growth. As industries increasingly demand customized products, injection molding is adapting to meet diverse consumer needs. Advances in materials science will facilitate the creation of more specialized plastics, allowing manufacturers to explore new applications. The trend toward sustainable production methods is expected to gain momentum, leading to more eco-friendly alternatives in plastic sourcing and production.
Automation will undoubtedly play a critical role, with manufacturers looking to integrate AI and machine learning to optimize processes and enhance production efficiency. The collaboration between manufacturers and technology providers will spur further advancements, enabling businesses to stay competitive and meet evolving market demands.
Understanding the intricacies of this process allows businesses to harness its advantages, leading to enhanced efficiency, innovation, and sustainability in production. With continued advancements in technology and materials, injection molding is positioned to remain a vital part of modern manufacturing.
Was this news helpful?