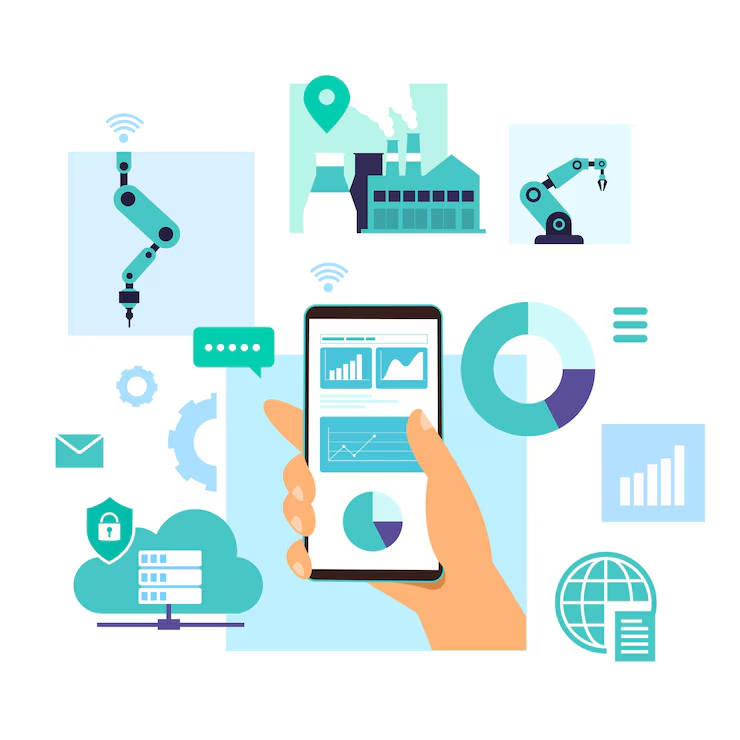
Explore how IoT is transforming manufacturing with five innovative use cases and upcoming trends for enhanced efficiency and quality control.
Manufacturing operations are being transformed by the Internet of Things (IoT). Manufacturers can use data and insights to drive efficiency, quality, and flexibility by connecting machines, systems and assets to the Internet. In this article, we look at five of the top use cases for IoT in manufacturing today, and upcoming trends that demonstrate how powerful this technology is going to be.
Optimizing Overall Equipment Effectiveness with IoT
Manufacturing metric overall equipment effectiveness (OEE) is an important metric that promotes holistic performance by measuring availability, performance rate and quality rate. With IoT sensors and connectivity at the machine level, manufacturers can now monitor OEE in real time and identify loss and inefficiencies as they happen.
This enables issues to be quickly addressed before small stops snowball into extended downtime. It also provides the data to uncover the root causes of systemic losses. With IoT and manufacturing software development services, connectivity and data exist to optimize processes, prevent recurring issues, and maximize OEE across production.
- Example: Tesla uses IoT sensors and data analytics to monitor workstations, machinery, and production flows closely. This allows them to maximize production quality and output, which helps them achieve their industry-leading gross margins.
Predictive Maintenance Prevents Downtime
Unexpected machine failures lead to expensive downtime that halts production. With IoT sensors monitoring everything from vibration to temperature fluctuations, manufacturers can catch issues before they occur through predictive maintenance. IoT manufacturing makes it possible to estimate when failures are imminent based on data patterns and alerts, allowing parts and services to be lined up ahead of time.
This prevents costly downtime and enables more strategic maintenance scheduling. As IoT use cases in manufacturing are implemented more broadly across plants, the volume of data will improve failure predictions over time. This evolution toward prescriptive guidance will minimize maintenance costs.
- Example: Food producer Nestle uses IoT for predictive maintenance across its many factories and machines.
Automating Inventory, Orders and Supply Chain with IoT
One should know what raw materials and parts are in hand and what input materials will be required for future production plans. IoT solutions for manufacturing offer real-time inventory and supply chain visibility. RFID tags track the materials, while sensor-enabled storage containers are self-monitored for stock levels.
The IoT system can also automatically order new stock or alerts buying managers to place the orders once certain inventory inventory thresholds are reached. It helps minimize inventory overhead costs incurred from manual inventory management and order placement, and eliminates stock outs that would cause downtime. IoT automation brings stability to supply chains that are becoming more complex.
- Example: Global logistics company DHL uses smart warehouses powered by IoT with sensors to monitor inventory levels, track shipments, and optimize storage. This system has increased order accuracy by 95%, reduced operational inefficiencies, and allowed predictive restocking to prevent disruptions in its supply chain.
Increasing Quality Control Efficiency with IoT
Defective products that reach customers can catastrophically harm brands and bottom lines. Manufacturers can expand quality control very much with the aid of IoT. Sensors can discover anomalies and outliers in production processes, which are indicators of potential quality issues. Computer vision can also process huge volumes of images to inspect for visible defects, and images can also be captured to inspect for visible defects.
Alerts trigger proper containment procedures when quality issues are identified. Aggregate quality data allows pinpointing of the systemic root causes of quality flaws so that these can be addressed at source. It protects the brand while improving yields.
- Example: In its manufacturing plants, BMW uses IoT based computer vision system to perform quality inspection on vehicle assembly lines. High accuracy defect detection is achieved using these systems since defects such as misalignments or paint irregularities are detected in a timely manner and rework rates are reduced.
Enhancing Worker Safety with Wearables and Sensors
Today industrial accidents still occur, but protecting worker health and safety is paramount. New mechanisms are provided by IoT for manufacturing to avoid preventable incidents. Air quality, temperature changes and chemical leaks can all be monitored with environmental sensors, and wearable devices can relay biometric indicators and worker proximity to hazards.
The IoT technologies detect dangerous conditions right away and activate safety measures. Further data analytics aid safety managers in understanding trends and patterns of accidents and how to control and train for risk.
- Example: Smart badges that track workers’ locations and detect exposure to harmful gases like hydrogen sulfide are among the smart wearables BP, an oil and gas company, implemented in its refineries. Emergency response time has been improved as well as safety compliance and these systems have drastically reduced workplace accidents.
The Road Ahead: Upcoming IoT Trends in Manufacturing
The manufacturing applications outlined above only scratch the surface of IoT’s potential. As technology and adoption continue evolving quickly, IoT systems will unlock more transformative capabilities:
Mainstreaming of AI-Enabled IoT Infrastructure
Today, IoT produces massive datasets, more than can be easily interpreted to derive value. As artificial intelligence becomes pervasive in manufacturing Internet of Things platforms, gaining insights from data will become automated. AI will guide notifications, recommendations and automated actions fueled by IoT data, replacing guesswork with predictive intelligence over time.
Mesh Networks Will Expand Connectivity
While many machines and assets are now IoT-enabled, connectivity can still be impacted by distance and obstructions in factories. The evolution toward mesh networks will eliminate these barriers, allowing devices to connect through proximity as data hops from one access point to the next automatically until reaching central systems. Ubiquitous connectivity will follow.
Simulation and Digital Twin Creation
Digital twins are virtual replicas of physical machines, infrastructure and even entire manufacturing plants. As IoT in manufacturing industry collects volumes of data on system performance and conditions, simulation tools can leverage this to create living digital twins that mirror almost real-time status and behavior. This will enable remote monitoring, simulation of changes, troubleshooting and more.
More Strategic Workforce Augmentation
IoT and associated data analytics will produce insights that transform workforce utilization over time. Manufacturers can deliberately acquire and train employees depending on real-time needs shown in the data, as the systems reveal process optimization possibilities and areas of a capability gap. This more responsive workforce planning will reduce overhead and drive productivity.
Closed Loop Quality
While today’s IoT for quality control identifies issues as they arise, closed-loop quality management will use data to pinpoint root causes further upstream, implement fixes systematically, and validate that fixes are working. This complete lifecycle approach would not only lower quality problems and increase yields but also streamline procedures to prevent like problems from reoccurring.
Conclusion
The Internet of Things manufacturing applications outlined in this article are only a precursor to the sweeping operational transformation promised by the Internet of Things in manufacturing. As smart machines, assets and systems seamlessly connect and communicate, they will unlock incredible visibility across factories and the entire supply chain.
Data and artificial intelligence will drive smarter decisions, enhanced training, and precise strategic adjustments dynamically. The result, for manufacturers that fully embrace IoT’s capabilities, will be organizations that learn, evolve and optimize automatically over time. This journey has only just begun, but for forward-thinking manufacturers the future is brighter than ever thanks to IoT.
Was this news helpful?